Bluetooth Controlled Home Equipments: Basic about bluetooth: Bluetooth is a wireless technology standard for exchanging data over short distances (using short-wavelength UHF radio waves in the ISM band from 2.4 to 2.485 GHz) from fixed and mobile devices, and building personal area networks (PANs). Invented by telecom vendor Ericsson in 1994 Radio frequency communication (RFCOMM) The Bluetooth protocol RFCOMM is a simple set of transport protocols, made on top of the L2CAP protocol, providing emulated RS-232 serial ports (up to sixty simultaneous connections to a Bluetooth device at a time). The protocol is based on the ETSI standard TS 07.10. RFCOMM is sometimes called serial port emulation. The Bluetooth serial port profile is based on this protocol. RFCOMM provides a simple reliable data stream to the user, similar to TCP. It is used directly by many telephony related profiles as a carrier for AT commands, as well as being a transport layer for OBEX over Bluetooth.
Posts
Showing posts from March, 2017
- Get link
- Other Apps
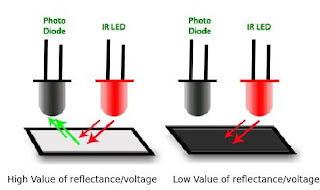
Line follower car : Aim: Create Arduino based Line follower robot from scratch. It is a machine that follows a line, either a black line on white surface or vise-versa. For Beginners it is usually their first robot to play with. In this tutorial, we will teach you to make the line follower robot move on the line with a type of feedback mechanism. It’s the most basic example of adding small intelligence to a robot, but it’s actually the designer’s intelligence!! Requirement: 1) Arduino Uno + Arduino IDE 2) DC geared motors x 2 3) Power bank or 9v or 12v Battery 4) IR sensors (ready made or You can make it by your own) 5) Connecting wires 6) Motor driver ready made or Your own. Working of sensors: IR light is invisible to human eyes it can be detected using IR sensore. As shown in picture below IR LED which is act as Transmitter and Photo Diode act as receiver. When Infrared Light strike on white surface its get reflect back and received by photo diode, while in ot